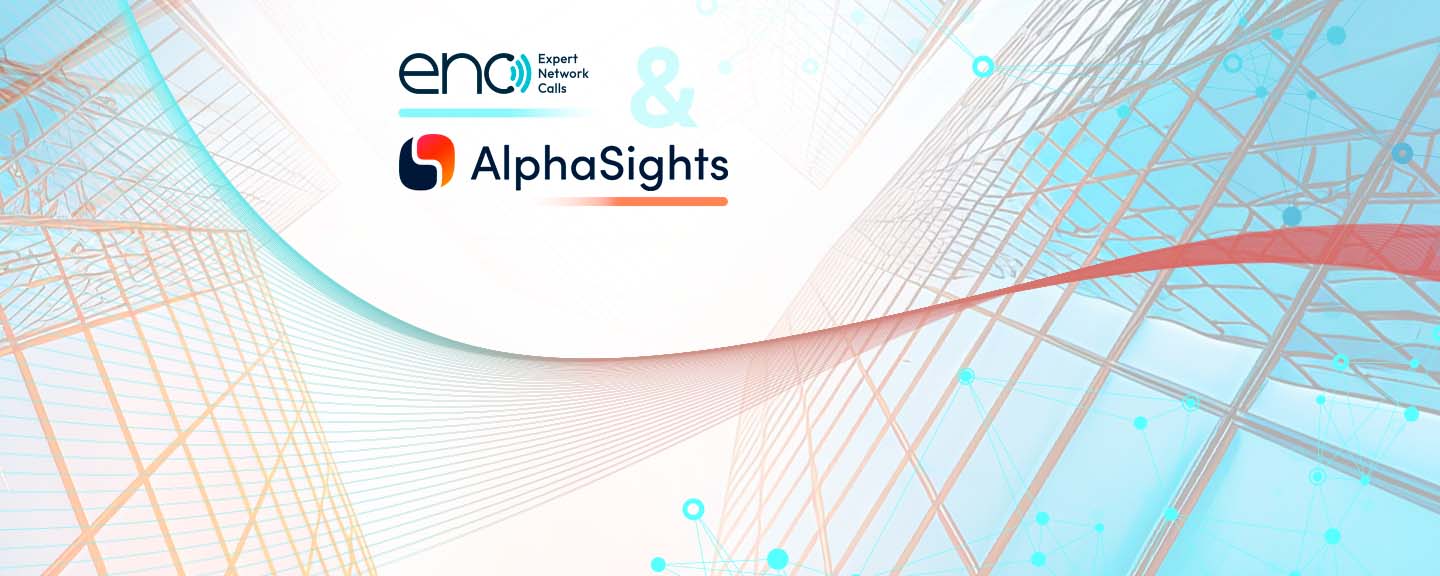
The term ‘digital twin’ is by no means new, but, in combination with the advances in artificial intelligence, its role in revolutionizing industrial processes and generating new economic value could significantly grow. From saving the amount of money required to roll out full-scale industrial processes to minimizing risks and preventing failures, this technology is considered to be one of the drivers of Industry 4.0.
What is a digital twin?
A digital twin is a virtual model, a probabilistic simulation of a physical object, process, or system. It is used to simulate, analyze, and predict real-world performance and problems by analyzing data from various sources, such as sensors and IoT devices. Using this cutting-edge technology, experts can better understand and manage real-world objects, which makes it easier to optimize, troubleshoot, and improve them.
Digital twin in a nutshell (video)
What is Industry 4.0?
The term ‘Industry 4.0’ describes the 4th industrial revolution, which is defined by the incorporation of cutting-edge digital technology such as AI and the Internet of Things (IoT) into industrial production processes. This stage of manufacturing marks a change from conventional industrial methods to automated, intelligent, and networked processes.
What are the applications of digital twins in manufacturing?
A digital twin is a virtual duplicate of a warehouse, facility, equipment, physical product, or system, developed from data collected in real-time through sensors and IoT devices. In smart manufacturing, the digital twin technology builds virtual replicas of goods, production lines, and even entire factories. As a result, manufacturing and product development become more efficient. In a virtual 3D environment, it also permits the modification and production of items.
Here are a few examples of digital twin technology being used in manufacturing:
- Digital twins track the functionality and state of machinery in real time to forecast maintenance and repair.
- Digital twins are used for real-time monitoring of quality and flaws.
- Digital twins can facilitate the on-demand manufacture of customized items by optimizing production processes in real time.
- Digital twins can help identify issues and suggest recovery steps whenever there is an error in the system.
- Since digital twins examine process data, they can show where the process can be improved or optimized.
- To guarantee adherence to certain regulations, digital twins can offer an in-depth record of operating conditions.
What effect does AI have on digital twins?
According to the latest forecasts, the AI industry is expected to grow to about two trillion dollars by 2030. AI and digital twins can collaborate in a number of ways, with AI considerably increasing the abilities of the technology in question.
- AI uses data from the digital twin to forecast when equipment could fail, thereby saving downtime.
- AI uses the digital twin to simulate and determine the most effective ways to operate machinery or processes.
- AI keeps an eye out for odd patterns in the digital twin to spot possible issues before they arise.
- The digital twin can analyze real-time data thanks to AI, which facilitates quick decision-making for operational improvements.
- Because digital twins gather a great deal of data, they can potentially be used to train AI and could even contribute to the creation of generative AI systems.
Case study: Real-life use of digital twins
To assist its operations, the well-known Mars Corporation has developed a digital twin of its manufacturing supply chain. Thus, thanks to Microsoft Azure's AI and IoT solutions, the company can process and analyze data collected by production machines to improve production margins, reduce waste, and empower real-time decision-making.
The corporation intends to leverage digital technologies to further infuse intelligence into the entire supply chain process. This will involve utilizing digital simulations to determine the best way to manufacture products while accounting for climate change and other situational factors, as well as improving transparency and visibility throughout the supply chain.
The challenges of using digital twins
While there are many benefits to digital twin technology, there are also common problems that companies using it currently face, with the major ones being:
- High implementation costs, rising power and storage needs, difficulties integrating it with current systems, and architecture intricacy.
- The necessity of modernizing outdated IT infrastructure and the difficulties with connectivity and the security of important information.
The process of setting up a digital twin technology is expensive and necessitates considerable investments in infrastructure creation, upkeep, data quality management, security solutions, and technological platforms (programs, sensors).
What does the future hold for AI-enabled digital twins?
Powered by artificial intelligence, digital twin technology appears to have a bright future in manufacturing and is expected to revolutionize the industry in a number of ways.
Among other things to expect from AI-enabled digital twins are:
- Producers will be able to swiftly and effectively emulate and experiment with a broad spectrum of designs and configurations, which will enable more advanced product customization.
- Through ongoing data analysis, AI-enabled digital twins will optimize industrial processes, increasing efficiency, decreasing waste, and saving money.
- The technology will go beyond the factory floor and optimize the whole supply chain, from the procurement of raw materials to the shipment of the final product, guaranteeing increased responsiveness and efficiency.
- Improved virtual environments through AI-powered digital twins will enable simulations of numerous situations with no risks related to real-life training and will eventually increase employee security and training.
- The technology will be essential to sustainability by helping producers cut their energy consumption and carbon impact.
- Anticipate a higher degree of integration with other cutting-edge technologies such as blockchain, augmented reality, and 5G, which will improve security, cooperation, and the overall potential of digital twins.
- Finally, with the help of digital twins, teams from all over the world will be able to collaborate more easily and scale operations more successfully.
Stay tuned for more industry and hi-tech news and content with Expert Network Calls.